What is Quality Management?
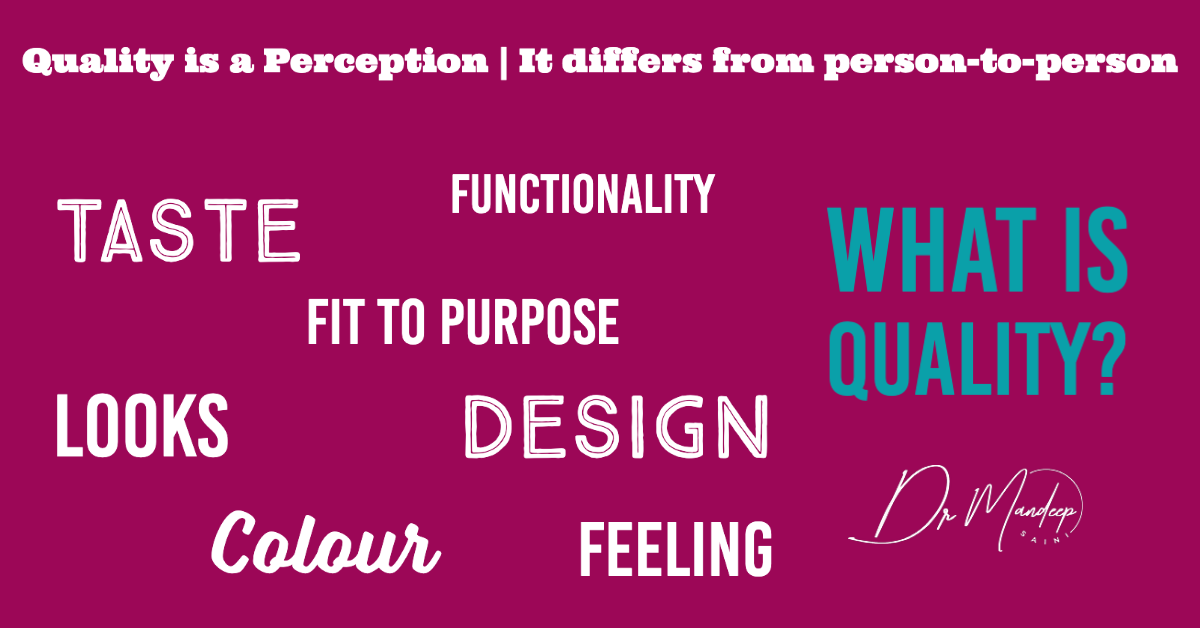
- What is Quality Management?
- Why is Quality Management Important?
- What are the benefits of Quality Management?
- What are the key elements of quality management?
- How can you implement quality management in your business?
- Quality management tools and resources
The process of quality management involves various steps and actions that help organisations to ensure that their products and services meet the needs of customers and conform to applicable regulatory requirements.
It is a process that encompasses all activities from the initial planning stage through to delivery and post-delivery support. The main aim of quality management is to provide organisations with a framework for continuous improvement for customer satisfaction. There are several different approaches to quality management, but all share the same basic principles.
This article will give you an overview of quality management and its key concepts.
Why is Quality Management Important?
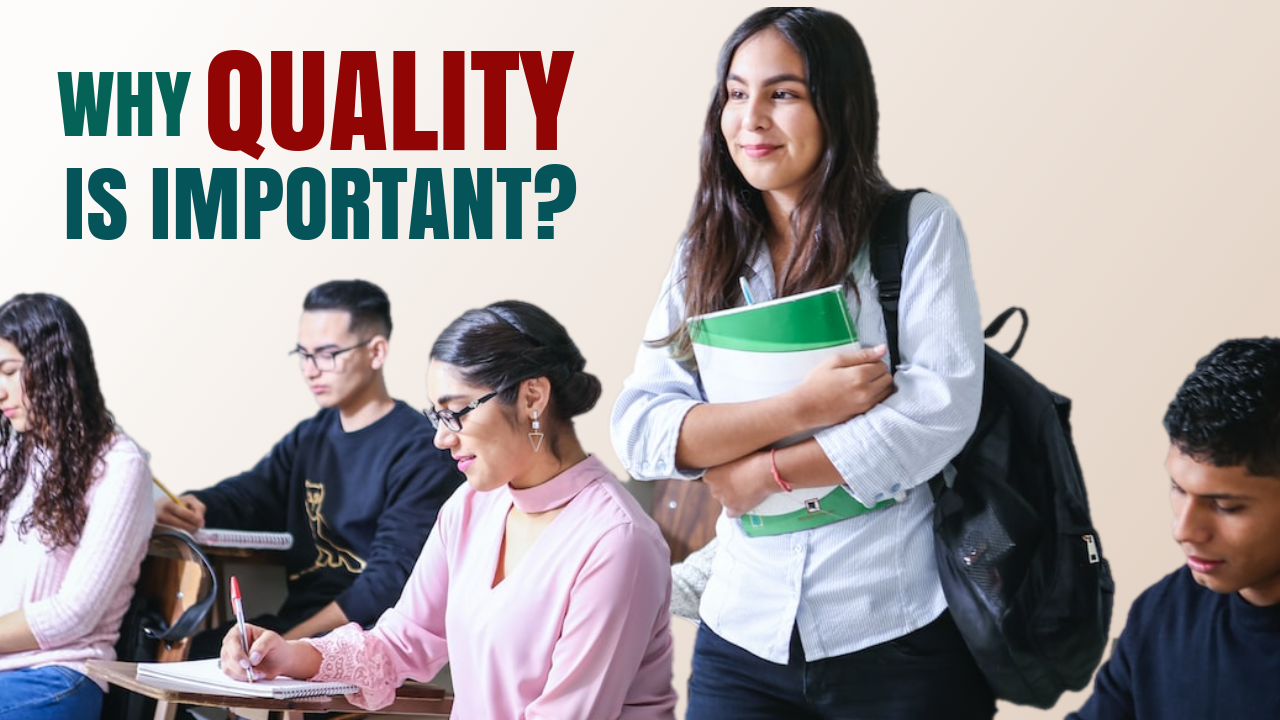
Quality management is important for organisations of any size. It ensures customer satisfaction, increases employee productivity, reduces waste and costs, and improves business performance.
In today’s competitive markets, organisations must stay ahead and provide superior products and services. Quality management helps organisations to develop and maintain consistent, reliable, and safe processes to ensure quality output.
It also helps organisations to identify and address potential quality issues before they become more severe and to meet customer requirements quickly and efficiently. Quality management helps an organisation to identify improvements that can be made to existing products, processes, and services and to develop new offerings that meet customer needs and expectations.
Organisations that invest in quality management will benefit from increased customer loyalty, improved reputation, and greater employee engagement, retention, and productivity. Ultimately, businesses that invest in quality management can better compete in the market, resulting in greater profits and long-term success.
What are the benefits of Quality Management?
Quality management offers organisations several benefits. By investing in quality management, organisations can:
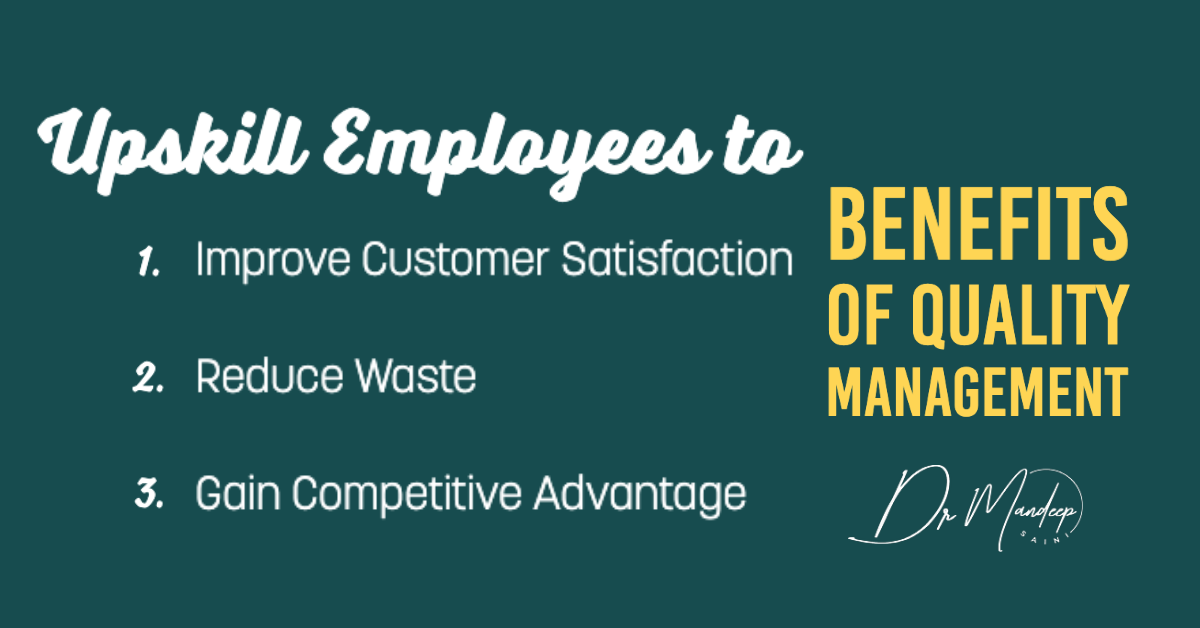
Improve Satisfaction: In order to ensure utmost customer satisfaction, it is of utmost importance to consistently deliver reliable and trustworthy products and services that not only satisfy their needs but go beyond their expectations. This requires a deep understanding of the customers’ preferences and requirements, as well as a commitment to continuously improve and innovate in order to meet their evolving needs. By providing exceptional products and services, businesses can establish a loyal customer base and create a positive reputation in the market..
Reduce Waste: To make your business more productive and profitable, you should review your processes and look for any problems that slow things down. This can help you save money by reducing waste and getting products or services to market faster. By making operations more efficient and eliminating problems, you can make the most of your resources and succeed in the long term.
Involve Employees: Promoting a workplace culture that values quality can deliver numerous benefits to a company. Such a culture need employee engagement and job satisfaction while also enabling the organization to attract and retain skilled workers. Additionally, prioritizing quality enhancement can result in improved productivity and overall success for the company.
Competitive Advantage: to stay ahead and make more money, it’s important to quickly and effectively meet customer needs. If you don’t, you could miss out on business and harm your reputation, which could hurt your long-term success. So, make sure you focus on making customers happy and communicating well.
Investing in quality management is a wise decision for any organisation. Quality management helps businesses to reduce costs, stay competitive, and maximise customer satisfaction by providing the best products and services on the market. Improving quality management processes and procedures can lead to greater profitability and long-term success.
What are the key elements of quality management?
Quality management is a process-oriented approach to managing process performance and continuous improvement. The four critical elements of quality management are:
- Quality Planning – defining planning for quality” When we talk about planning for quality, we are referring to developing strategies and methods to ensure that a product or service meets certain standards of excellence. This involves identifying the key features and characteristics that are important to customers or clients (Identifying customers’ needs), setting clear goals and objectives, and establishing a plan of action to achieve those goals. Effective planning for quality should come from the leaders. Effective planning can help improve efficiency, reduce waste, and enhance customer satisfaction, ultimately resulting in increased profitability and success for a business or organization.
- Quality Assurance – is a process that ensures products or services meet certain quality standards before releasing them to the public. Different tools and techniques are used to identify defects or issues (5 Why’s and Fishbone chart for root cause analysis) and address them before customers receive them. Businesses must ensure customers receive high-quality products and services that meet their expectations. This involves ensuring quality standards are being met and adopted throughout the organisation and that proper processes are in place for resolving quality issues.
- Quality Control – is an essential aspect of any production or manufacturing process. It ensures that the final product meets the required standards and specifications. Without proper quality control measures in place, there is a risk of producing defective products that can harm the end-users or damage the reputation of the company. Therefore, it is crucial to establish a robust quality control system that can identify and eliminate any defects or inconsistencies in the production process. By doing so, companies can ensure that their products are of high quality, safe, and reliable.
- Quality Improvement or Continuous Improvement – It is crucial for any organization to actively seek ways to improve its quality standards and processes. One effective approach is to utilize methodologies such as Kaizen and Poke Yoke. These methods allow for the identification of errors and inefficiencies, which can then be addressed through the implementation of changes aimed at improving overall performance. By regularly reviewing and refining processes, an organization can ensure that they are operating at its highest level of efficiency and effectiveness.
These four key elements form the foundation of quality management, allowing organisations to achieve process excellence and superior product and service quality. Implementing quality management in an organisation encourages better cost control, improved customer satisfaction, and increased product and service quality.
How can you implement quality management in your business?
Implementing quality management into any business should be a top priority, as it will help ensure success and customer satisfaction. Here are five steps to implementing quality management in your business. But don’t forget to look at Demming’s, Juran’s and Crosby’s work.
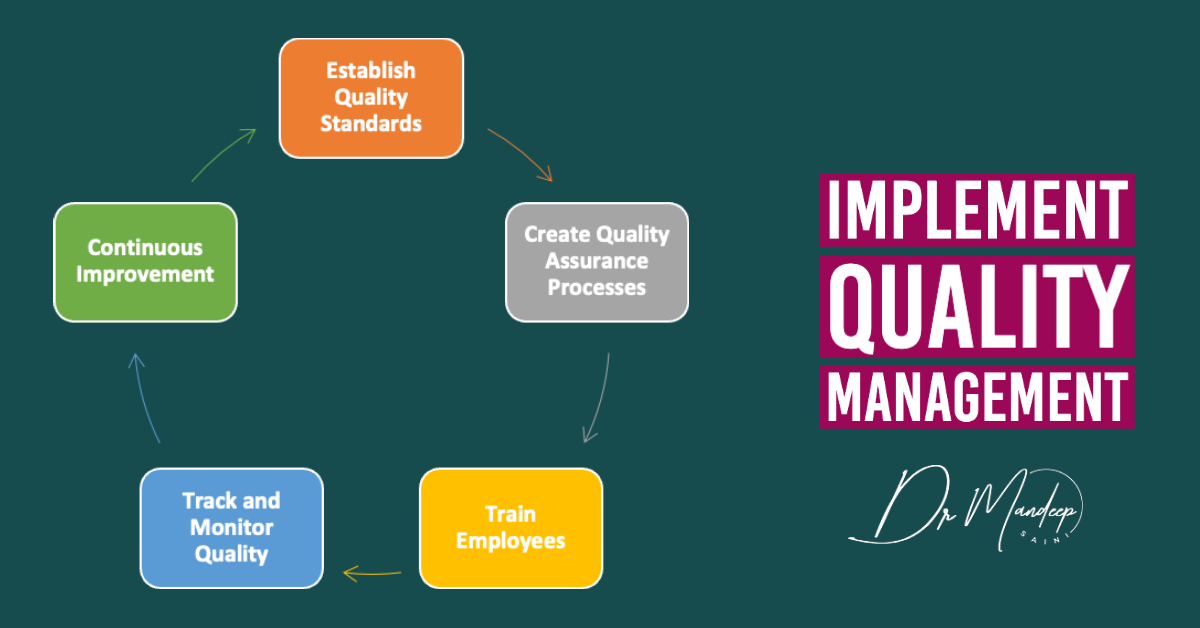
- Establish Quality Standards – you should develop a set of guidelines and standards that will be used to measure a product or service’s quality. To make sure your product or service is high-quality, you need to figure out what that means for your specific situation. Look at industry standards (ISO 9000), and customer feedback (Voice of Customers), and talk to experts. Then, create standards and goals that you can measure to make sure you meet those quality standards (Benchmarking). Check regularly to see where you can improve and make changes over time to keep up with the standards (Continuous Improvement). Keep working to improve and be willing to change as needed.
- Create Quality Assurance Processes – Establishing formal processes for reviewing and testing products and services to ensure that they consistently meet their quality standards. This will help create reliable and effective quality assurance processes. You should establish a formal processes for reviewing and testing products and services to ensure they always meet their quality standards.
- Train Employees on Quality Management Practices – Training employees on quality management practices is essential for maintaining high work standards. Through this training, employees can learn about established quality standards and processes, ensuring they maintain the highest level of quality in their work. Educating employees on quality management practices benefit both the organization and its workers. You must train them (See Deming’s 14 points of Quality Management) on the established quality standards and processes to ensure they are set to work to the highest standards.
- Track and Monitor Quality metrics – To make sure things are done well, it’s a good idea to have a system for keeping track of quality. This helps you find problems quickly and fix them fast. Doing this can make your organization work better and give better results. Therefore you should develop systems to track and monitor quality metrics (i.e. House of Quality) to detect any issues and take appropriate actions quickly.
- Provide Continuous Improvement Opportunities– Implement systems for actively seeking customer feedback, reviews, and other data to help identify improvement areas. Moreover, seek improvement in the above four points.
Quality management tools and resources
Once you have established quality standards and processes and trained your employees, you must equip them with the right tools and resources to ensure they have all they need to keep your quality standards high. Quality management is a continual process, so here are some tools and resources that can help you:
Process Mapping – Process mapping can help create clear visual representations of your processes and quality management plans so everyone is on the same page.
Quality Review Checklists – Having checklists for quality reviews can help ensure that all key elements are covered when evaluating products.
Quality Assurance Documentation – Documenting the quality assurance processes and the test criteria can be valuable for tracking and monitoring quality metrics.
Quality Improvement Templates – Templates can be used to record feedback from customers and other stakeholders to identify areas for improvement.
Risk Management Training – Having employees trained in risk management can help them identify potential risks to product quality before they become a problem.
-
Digital Supply Chains
The term “digital supply chain” refers to the many connections between a company and other companies to get their products from one place to the other. Read more
-
How to use examples in academic writing?
Using examples in academic writing can make your writing more engaging and persuasive and clearly and concisely explain complex concepts. Read more
-
Applying for Part-Time Jobs in the UK
When it comes to applying for a part-time job in the UK as an international student, having a well-written CV and cover letter is crucial. Read more
-
Top Part-Time Jobs for International Students in the UK
Part time jobs in uk for international students, What part-time jobs are available and how to get it. Read more
-
How to search for part-time jobs in the UK?
How to search for part-time jobs in the UK? Looking for part-time jobs as an international student in the UK can be challenging, but it’s not impossible. Read more
-
Finding Part-Time Jobs in the UK
According to the UK government website, students on Tier 4 (General) student visas can work up to 20 hours per week during term-time and full-time during scheduled breaks (such as the Christmas and Easter holidays) and after finishing their studies. Read more