Inventory Types and Demand Management
In the complex global supply chain management world, understanding the nuances of inventory types and demand management is crucial for businesses seeking to streamline operations and reduce costs. This blog post delves into the vital aspects of inventory management, shedding light on strategies and tools essential for minimizing inventory within the supply chain.
The Significance of Inventory in Supply Chains
Inventory management poses a significant challenge in supply chains, often requiring intricate strategies to balance holding costs with demand fulfilment. As businesses evolve, shifting towards customer-centric models demands reevaluating inventory practices and emphasizing efficiency and customization.
The Evolution of Supply Chain Management
Historically, supply chain management has undergone significant transformations, from the basics of global supply chain understanding to embracing the advancements of Industry 4.0 and 5.0. Concepts such as lean management, resilience, and the bullwhip effect have shaped current practices. The latest trend focuses on aligning supply chains closely with customer demands, aiming for the right product in the right quantity at the right time and place.
Inventory Types and Their Impact
Inventory is not just about finished goods; it encompasses raw materials, components, and work-in-process items. Each type of inventory carries associated costs, including storage, handling, and opportunity costs. Traditional inventory practices often result in excess holdings, leading to increased expenses and inefficiencies.
Raw Materials
Essential for production but require careful management to avoid overstocking.
Definition: Raw materials are the essential components or primary inputs required to manufacture products. They form the base of the production process and can include anything from metals, plastics, and textiles to electronic components and chemicals. For instance, Consider a furniture manufacturing company that specializes in wooden tables. The raw materials for this company include wood (such as oak or pine), adhesives, paints, and varnishes.
Management Challenge: The key to managing raw materials effectively is to avoid overstocking, which can tie up capital unnecessarily and increase the risk of spoilage or obsolescence, especially for materials with a shelf life. For the furniture company, overstocking on specific types of wood could lead to issues if market trends shift toward different materials or designs, potentially leaving the company with a surplus of unwanted stock.
Work-in-Process
Represents goods in the production phase, which need optimization to ensure smooth flow and reduce bottlenecks.
Definition: Work-in-process refers to materials partially converted through the manufacturing process but not yet completed products. WIP includes items currently being fabricated, assembled, or undergoing processing. For example, in the context of the same furniture manufacturing company, WIP inventory might include table tops that have been cut and shaped but not yet sanded, painted, or assembled with legs.
Management Challenge: The main challenge with WIP inventory is ensuring a smooth flow through the production process to reduce bottlenecks and inefficiencies. For instance, if the sanding department is overwhelmed and cannot handle the volume of table tops from the cutting section, it creates a bottleneck that delays subsequent stages like painting and assembly. Optimizing each stage’s production schedule and capacity is crucial to managing WIP effectively.
Finished Goods
Demand accurate forecasting to meet customer demands without overproducing.
Definition: Finished goods are the final products ready for sale to customers. These products have completed the manufacturing process and are awaiting purchase. For Instance, for our furniture company, finished goods consist of completed tables that are fully assembled, painted, and varnished, ready to be shipped to retailers or direct customers.
Management Challenge: The primary challenge with finished goods is accurate forecasting to meet customer demand without overproducing. Overproduction leads to excess inventory, increased storage costs, and potential markdowns to clear unsold items. For example, if the furniture company anticipates a high demand for oak dining tables and produces a large quantity, but customers prefer pine or a different style, the company will be left with a surplus of oak tables. Accurate demand forecasting, perhaps through market analysis and past sales data, can help the company produce closer to the actual demand, minimizing the risk of excess inventory.
In determination, effective inventory management across raw materials, work-in-process, and finished goods requires a delicate balance between supply and demand. Companies must carefully manage their raw material stocks to prevent overstocking, optimize their production processes to smooth out WIP bottlenecks, and accurately forecast demand for finished goods to avoid overproduction. Achieving this balance is crucial for minimizing costs, maximizing efficiency, and ensuring the company can respond flexibly to market demands.
Strategies for Minimizing Inventory

The move towards mass customization and personalization has prompted businesses to adopt just-in-time (JIT) production models. This approach minimizes inventory levels, relying on accurate demand forecasting and agile supply chain practices to produce goods as needed, reducing the holding costs and risks associated with obsolete inventory.
Demand Management: The Cornerstone of Inventory Reduction
Understanding and predicting customer demand is fundamental in managing inventory levels. By distinguishing between dependent and independent demand, businesses can tailor their inventory strategies to meet actual needs, avoiding overproduction and excessive stockholding.
Dependent Demand: Directly related to the production of another item, such as components for a final product.
Definition: Dependent demand refers to items for which demand is tied directly to the production of another product. In other words, the need for these items directly results from the market for another item, typically a final product. These items are usually components or raw materials needed for manufacturing.
Example: Consider an automobile manufacturing company that produces cars. The demand for car tyres (the dependent item) is directly tied to the production of vehicles (the final product). If the company plans to manufacture 1,000 cars, and each vehicle requires four tyres, then there is a dependent demand for 4,000 tyres. The tyre’s market demand determines not the tyre demand but the number of cars the company plans to produce.
Management Challenge: Managing dependent demand involves precise planning and coordinating production schedules. Manufacturers must accurately forecast the market for the final product to determine the required quantity of components or materials, ensuring they have enough to meet production needs without overstocking.
Independent Demand: Not directly tied to another product’s production, reflecting the market’s demand for finished goods.
Definition: Independent demand is the need for finished goods or products not directly tied to the demand for other items. Market conditions, consumer preferences, and other external factors influence this type of demand.
Example: Using the same automobile company, the demand for the cars they produce is an example of independent demand. Consumers purchase cars based on various factors like brand preference, price, features, and personal needs. This demand is independent of the company’s production decisions for specific components (like the tyres in the dependent demand example) and is influenced by broader market trends.
Discover a world
of possibilities
Dive into an experience that sets us apart in an ever-evolving landscape.
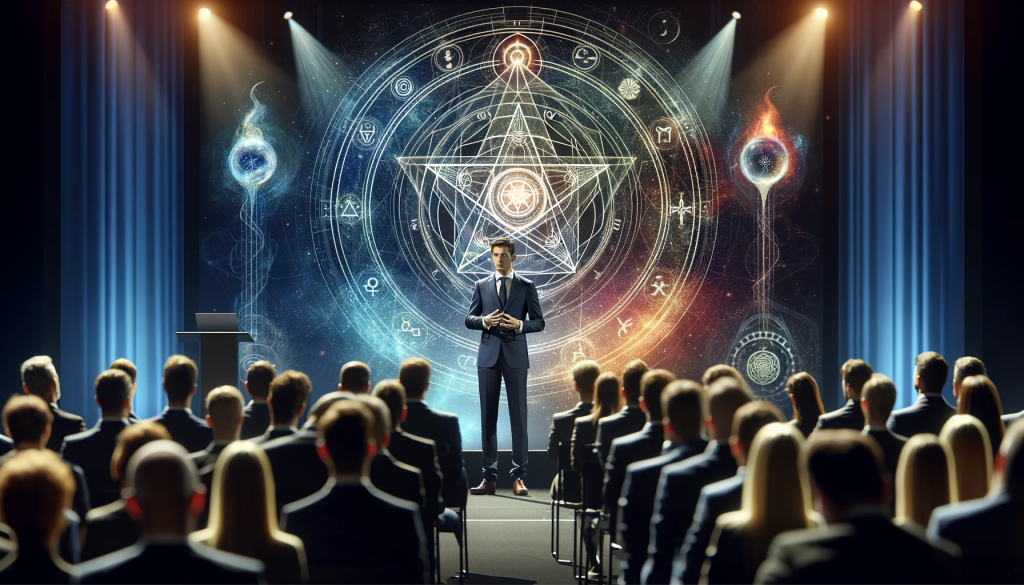
Management Challenge: Forecasting independent demand requires understanding market trends, consumer behaviour, and external factors such as economic conditions. Companies face the challenge of predicting how many finished products they will sell, directly affecting their production planning, inventory management, and procurement strategies. Overestimation can lead to excess inventory and increased holding costs, while underestimation can result in stockouts and lost sales.
Interplay Between Dependent and Independent Demand:
Understanding the interplay between these two types of demand is crucial for businesses. For example, the automobile company must accurately forecast the independent demand for its cars to determine the dependent demand for components like tyres, engines, and electronics. This synchronization ensures that the company maintains optimal inventory levels, maximizes efficiency, and meets customer demand without overproducing or incurring unnecessary costs.
In summary, dependent demand is directly related to the production of another item and requires careful planning to align with production schedules. On the other hand, independent demand is determined by market forces and requires accurate forecasting to meet consumer needs without overstocking or running out of stock. Both demand types are critical in supply chain management, influencing inventory levels, production planning, and overall business strategy.
The Role of Technology in Inventory and Demand Management
Advancements in technology, particularly in data analytics and AI, have transformed inventory and demand management. These tools enable more accurate forecasting, real-time tracking, and dynamic adjustment of inventory levels, further reducing waste and enhancing responsiveness to market changes.
Findings
Inventory and demand management complexities in global supply chains require a nuanced understanding and strategic approach. By focusing on efficiency, customization, and leveraging technology, businesses can significantly reduce inventory costs while meeting customer demands more effectively. The journey towards streamlined supply chains is ongoing, with continuous improvement and innovation at its core.