What is Total Quality Management
Introduction
Total Quality Management (TQM) is a business management approach that stresses continuous improvement of whatever we do. TQM is an approach that seeks to integrate all aspects of an organization that impact quality, from design and production to delivery and customer service.
TQM aims to improve the quality of products and services through a systematic and continual process of planning, monitoring, and improvement. TQM is a customer-focused approach that begins and ends with the customer.
To be successful, TQM must be implemented at all levels of an organization and involve all employees. Implementing TQM can be challenging, but the rewards are worth the effort. When done correctly, TQM can lead to increased customer satisfaction, improved quality of products and services, and increased profitability.
What is Total Quality Management (TQM)?
Total Quality Management (TQM) encourages all employees to be involved in the quality process. It identifies problems, works to reduce variation and waste, and is based on feedback from customers and employees.
The primary principles of TQM are:
1. Commitment to Quality: All employees, suppliers, and customers must be committed to delivering and receiving quality products and services.
2. Continuous Improvement: TQM aims to continually improve processes, products and services by overseeing data and feedback.
3. Customer Focus: Customers must come first and provide feedback that will help improve the process.
4. Employee Involvement: Everyone must be involved in identifying problems and solutions to maximize efficiency.
TQM is an integrated and comprehensive approach focusing on quality as a competitive advantage. Its goal is to maintain customer loyalty and maximize labour, resource and capital efficiency. By using TQM, companies can enhance their business performance and drive greater customer satisfaction.
The History of TQM
Total Quality Management (TQM) is not a new concept. It has its roots in the Total Quality Control (TQC) model, which W. Edwards Deming developed in the early 1950s. His philosophy was simple: if you focus on improving the quality of your products, you will improve your customer experience.
Many companies and government organizations around the world adopted Deming’s model. In the late 1980s, the Toyota Motor Company in Japan adopted the model and needed an acronym to differentiate it from other forms of total quality control. Thus, TQM was born.
Since then, the model has evolved. It includes process improvement, customer feedback, employee involvement and training, and supplier collaboration. Many successful organizations have adopted the model and used it as a part of their continual improvement process. The result is improved customer satisfaction, higher quality products, and a better bottom line.
The Benefits of TQM
Total Quality Management has proven to be a valuable tool for companies and organizations. Companies implementing TQM have seen increased customer satisfaction, product quality, and profitability. Many of these benefits are directly or indirectly related to TQM, such as:
1. Lower costs – Improving processes will increase efficiency and decrease waste, resulting in lower costs.
2. Improved customer relationships – When companies practice TQM, they focus on understanding the needs of their customers and strive to meet or exceed those expectations. This leads to increased customer loyalty and better customer relationships.
3. Increased productivity – By providing employees with the proper training and resources, companies can ensure that tasks are done correctly and efficiently. This, in turn, leads to higher overall productivity and fewer defects.
4. Enhanced innovation – By focusing on continuous improvement, employees can come up with innovative solutions for problems. This allows for developing new products or processes that can save time and money in the long run.
5. Increased employee satisfaction – Employee involvement is a key element of TQM, leading to increased engagement and motivation. This helps create an overall positive work environment, resulting in higher job satisfaction.
Implementing TQM
Implementing Total Quality Management (TQM) in an organization is no small task. It involves commitment from the entire organization to keep and maintain the quality standards. The following steps will help you get started on the process:
1. Assessing needs and setting objectives: The first step towards implementing TQM is to assess the organization’s existing needs and establish the desired objectives and goals.
2. Creating a quality management system: Building a system designed to meet the organisation’s needs and satisfy customer expectations.
3. Training employees: Training employees on the best practices of TQM and how these can be applied to the organization’s processes.
4. Establishing systems and improving processes: Establishing process flow charts that identify, measure, evaluate, and improve processes.
5. Monitoring results and measuring performance: Analyzing and regularly monitoring results to determine the success or failure of the quality management system and taking corrective action as required.
Total Quality Management can positively affect an organization, but it must be implemented correctly to be successful. With the right planning and resources, an organization can reap all the benefits of TQM.
TQM in the Workplace
When implemented in the workplace, Total Quality Management (TQM) helps organizations to optimize working methods, become more efficient and provide higher-quality products. TQM techniques ensure that all departments, from the production line to the customer service representatives, work towards the same goal.
There are six main steps to implementing TQM in the workplace:
1. Partner with stakeholders: First, it is important to partner with stakeholders to identify shared values and develop a shared understanding of quality goals.
2. Set goals and objectives: Set measurable goals and objectives that align with overall quality standards and values identified by stakeholders.
3. Develop and implement processes and procedures: To enable organizations to achieve their quality goals, develop and implement detailed processes and procedures.
4. Evaluate performance: Monitor performance and take corrective action as needed.
5. Monitor and improve quality: Regularly monitor and review quality and take steps to improve quality continuously.
6. Report results and progress to all stakeholders.
By implementing Total Quality Management in the workplace, organizations can reduce costs and increase customer satisfaction, ultimately leading to greater success.
TQM Tools and Techniques
Total Quality Management (TQM) has been adopted by organizations around the world, and it is effective when implemented correctly. To ensure success, organizations should use appropriate TQM tools and techniques. Here are some of the most common TQM tools and techniques used by organizations:
1. Process Flowchart – A Process Flowchart is used to map out processes and identify any areas of improvement.
2. Cause and Effect Diagram – The Cause and Effect Diagram is used to uncover and analyze the root cause of a problem.
3. Check Sheet – This is a simple tool used to collect data and identify any uncovered patterns or issues.
4. Control Chart – A Control Chart is used to analyze processes and monitor the quality of results.
5. Pareto Chart – The Pareto Chart is used to identify the most critical areas for improvement.
6. Histogram – The histogram presents data in an easy-to-understand way.
7. Scatter Plot – Scatter Plots are used to compare two variables and to identify any relationships.
These tools and techniques enable organizations to identify and improve processes, helping to ensure quality is maintained and improved.
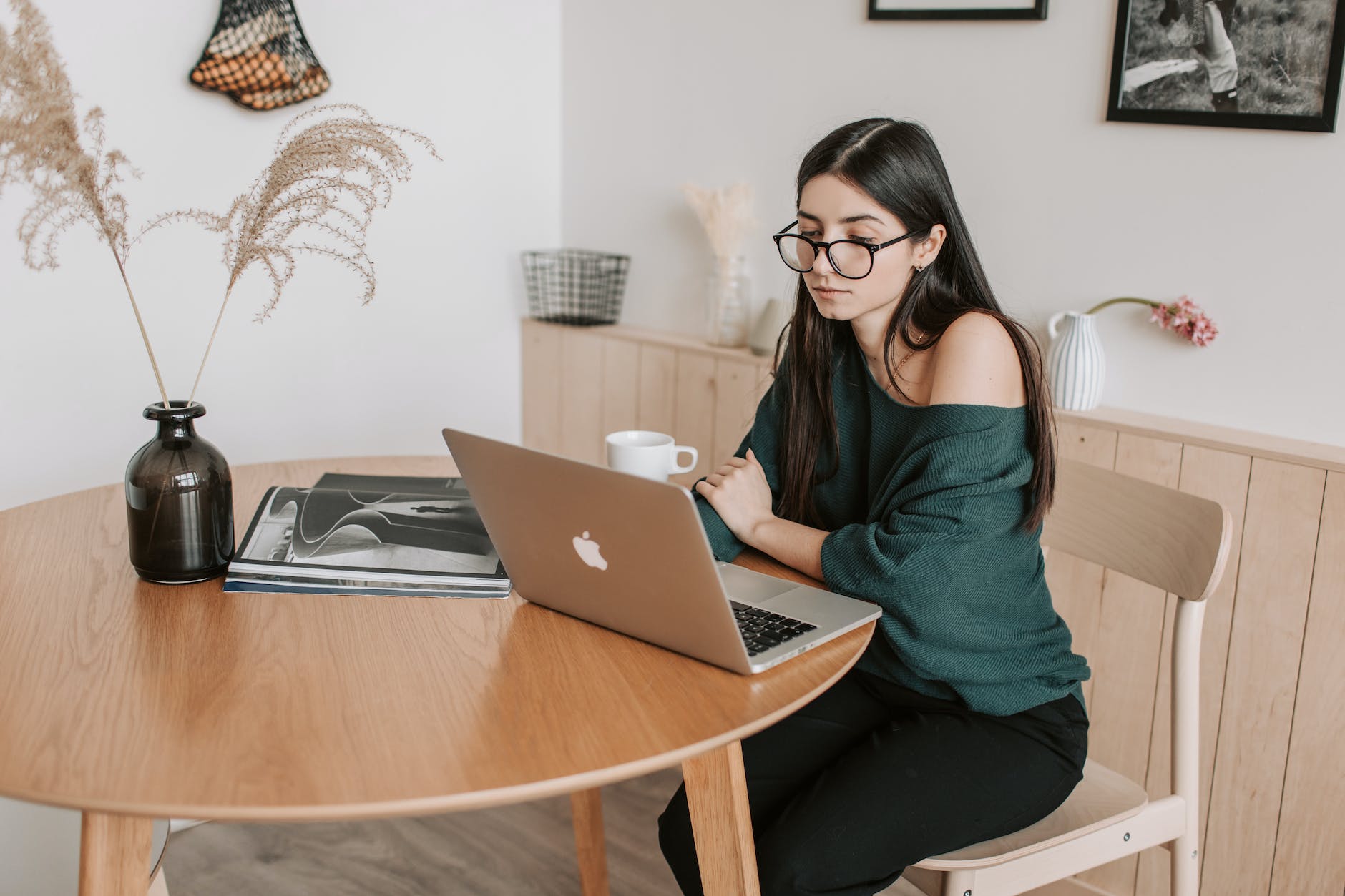
TQM Resources
In addition to the tools and techniques used with TQM, organizations must have specialized resources to ensure success. These resources are typically categorized into people, Materials, and Equipment.
People: Having the right people with the right skills and knowledge is a key component of TQM. It is important to have employees dedicated to the organization’s quality goals and a passion for excellence.
Materials: Quality materials are essential for TQM. Organizations should select high-quality products and materials for their projects and processes.
Equipment: Quality equipment is needed for accurate and reliable operations. Organizations should invest in high-end equipment and software to ensure their processes’ and data’s accuracy and reliability.
By understanding and utilizing the right tools, techniques, and resources, organizations can successfully implement TQM and obtain the desired results.
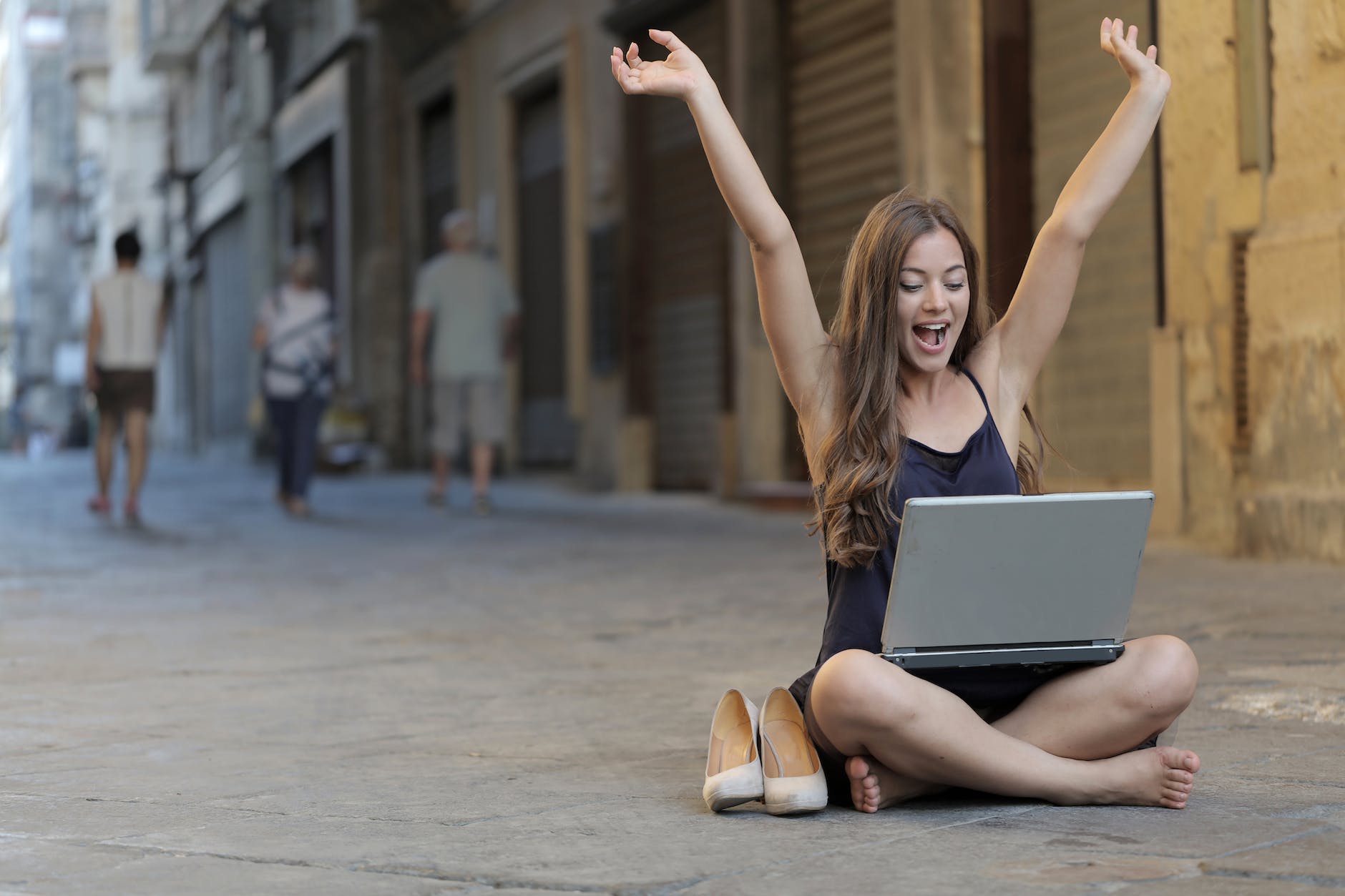
To Wrap Things Up
Total Quality Management (TQM) is an important concept for businesses because it helps lead to better quality products, reduced costs, and improved customer satisfaction. To successfully implement and maintain TQM, businesses need to understand the tools, techniques, and resources needed to implement and maintain TQM.
The tools, techniques, and resources outlined in this blog can help organizations understand and implement TQM. These tools, techniques, and resources include training, responsible leadership, quality assurance practices, data collection and analysis, and the right environment.
Additionally, organizations must understand the importance of investing in the right people, materials and equipment for their TQM initiatives. With the right tools, techniques, and resources, businesses can leverage TQM to achieve success.